Volume 08, Special Issue Department of Mechanical Engineering College, Pragati Engineering College, MAY 2022
-
Optimization of Support Structures to Minimize the Displacement Mr. V. Sandeep, Mr. P. Pavan Kumar, Mr. I. Akshay, Mr. K. Vinay Kumar, Mr. K. Sweet Babu, Mr. VVN Sarath, Mrs. P Gayatri
The purpose of this study is to study the influence of the laser power and the scanning speed on the surface hardness, and top surface and side surface roughness of Ti-6Al-4V metal specimens fabricated via the selective laser melting (SLM) technique. The laser power was varied between 150 and 300 W while the scan speed was varied between 800 and 1400 mm/s. Response surface methodology (RSM) in the Design Expert 11 software environment
Optimization of Support Structures to Minimize the Displacement of Standard ASTM E8 Tensile Specimen
Mr. V. Sandeep, Mr. P. Pavan Kumar, Mr. I. Akshay, Mr. K. Vinay Kumar, Mr. K. Sweet Babu, Mr. VVN Sarath, Mrs. P GayatriOptimization of Support Structures
-
Reconstruction and Segmentation Of Cancer Affected Patient's Lower Jaw Mr. Sai Aditya Vardhan Sanku, Mr. Naveen Gorsipudi, Mr. Aravind Gollapalli, Mr. Sashendra Srinivasa Baswanth Pappula, Mr. Pavan Sai Mattapalli, Mr. B Bharath Kumar, Dr G Avinash
Additive manufacturing is one of the latest manufacturing techniques which has the ability to generate complex parts. Our paper deals with application of this technique in the field of biomedical. This work concerns a type of bone cancer known as Osteosarcoma. A methodology has been proposed here in which Computer Tomography (CT) scan data is used to make a 3D model and the portion containing cancer is studied in Computer Aided Design
Reconstruction and Segmentation Of Cancer Affected Patient’s Lower Jaw
Mr. Sai Aditya Vardhan Sanku, Mr. Naveen Gorsipudi, Mr. Aravind Gollapalli, Mr. Sashendra Srinivasa Baswanth Pappula, Mr. Pavan Sai Mattapalli, Mr. B Bharath Kumar, Dr G AvinashReconstruction and Segmentation
-
Cad Modelling of Human Ankle from CT and MRI Scan to Study the Bone Mr. G.V.V. Satyanarayana, Mr. M. Venkata Ramana, Mr. P. Ganesh, Ms. S. Vakshika Kalyani, Mr. D. Apparao, Mr. B Hari Krishna, Mr. DJ Johnson
Recent findings show that 3DP is a versatile technology platform for numerous materials for mass customizable bone regeneration devices that are also getting approval from different regulatory bodies worldwide. After a brief introduction of different 3DP technologies, 3DP of different materials and devices for bone regeneration. From cell-based bioprinting to acellular patient-matched metallic or ceramic devices, 3DP
Cad Modelling of Human Ankle from CT and MRI Scan to Study the Bone
Mr. G.V.V. Satyanarayana, Mr. M. Venkata Ramana, Mr. P. Ganesh, Ms. S. Vakshika Kalyani, Mr. D. Apparao, Mr. B Hari Krishna, Mr. DJ JohnsonCad Modelling of Human Ankle from CT
-
Experimental Investigation on Effect of Layer Width on Dimensional Ms. D. Deeksha kanaka Lakshmi, Ms. K. Maheswari, Mr. N. Naga babu, Mr. C. Sunil, Mr. A.Vivek, Ms. K Tulasi, Mr M Sunil Raj
3D printing is emerging technology in advance manufacturing process. The main moto of the 3D printing is to achieve the most complex geometries accurately without effecting the features of the object within less time compare to conventional manufacturing. To build any component we need material and power source. Materials used in 3d printing are polymers, metals powders, ceramic powder etc… Material consumption
Experimental Investigation on Effect of Layer Width on Dimensional
Ms. D. Deeksha kanaka Lakshmi, Ms. K. Maheswari, Mr. N. Naga babu, Mr. C. Sunil, Mr. A.Vivek, Ms. K Tulasi, Mr M Sunil RajExperimental Investigation on Effect
-
Analysis of G-Code on FDM Build Parts to Achieve the Exact Height of CAD Model Mr. R. Venkata Siva Subrahmanyam, Ms. V. Veera Durga Chishma, Mr. CH. Dorababu
Additive manufacturing is the process of creating an object by building it one layer at a time. It is the opposite of subtractive manufacturing, in which an object is created by cutting away at a solid block of material until the final product is complete. Not every manufacturing process is the 100% efficient. In additive manufacturing also we have problems take care off before printing the model. Out of all the machine
Analysis of G-Code on FDM Build Parts to Achieve the Exact Height of CAD Model
Mr. R. Venkata Siva Subrahmanyam, Ms. V. Veera Durga Chishma, Mr. CH. DorababuAnalysis of G-Code on FDM Build Parts
-
Analysis of Effect of Process Parameters On Fused Deposition Modeling (FDM) Technique Mr. M. Sai Venkata Srinivasa Reddy, Ms. G. Rama Laxmi, Ms. T. Meghana, Ms. B.Manogjna
Rapid prototyping is a manufacturing process in which a computer-aided design (CAD) model is used to fabricate a physical model without the use of fixtures, tools, and human intervention. The prototype is made by deposition of material in layers. The major advantage of this manufacturing process is that it can fabricate complex part quickly with minimum loss of material. There are many rapid prototyping techniques available commercially
Analysis of Effect of Process Parameters On Fused Deposition Modeling (FDM) Technique
Mr. M. Sai Venkata Srinivasa Reddy, Ms. G. Rama Laxmi, Ms. T. Meghana, Ms. B.ManogjnaAnalysis of Effect of Process Parameters
-
Design and Analysis of Camshaft & Development of CAM Code for Die Manufacturing Mr. CH. Venkata Ramana, Mr. V. Pavan Kumar, Mr. P. Sanjay Joshi, Mr. G. Ganesh Swamy, Mr. S. Danish Hameed, Mr. GVN Santosh, Dr BSV Ramarao
The camshaft and its associated parts control the opening and closing of the two valves. The associated parts are push rods, rocker arms, valve springs and tappets. This shaft also provides the drive to the ignition system. The camshaft is driven by the crankshaft through timing gears. Cams are made as integral parts of the camshaft and are designed in such a way to open the valves at the correct timing and to keep them open
Design and Analysis of Camshaft & Development of CAM Code for Die Manufacturing
Mr. CH. Venkata Ramana, Mr. V. Pavan Kumar, Mr. P. Sanjay Joshi, Mr. G. Ganesh Swamy, Mr. S. Danish Hameed, Mr. GVN Santosh, Dr BSV RamaraoDesign and Analysis of Camshaft
-
Modeling and Damping Analysis of High Grade Steel Alloy Drive Shaft in Automobile Ms. CH. Sravani Jyothi Varalakshmi, Mr. K. Sri Satish Chandra, Ms. M. Bhavana Sri, Mr. J. Satish Charan
A drive shaft is a mechanical component for transmitting torque and rotation, usually used to connect other components of a drive train that cannot be connected directly because of distance or the need to allow for relative movement between them. As torque carriers, drive shafts are subject to torsion and shear stress, equivalent to the difference between the input torque and the load. The functions of the driveshaft
Modeling and Damping Analysis of High Grade Steel Alloy Drive Shaft in Automobile
Ms. CH. Sravani Jyothi Varalakshmi, Mr. K. Sri Satish Chandra, Ms. M. Bhavana Sri, Mr. J. Satish CharanModeling and Damping Analysis of High Grade
-
Development and Reconstruction of Spinal Cord from CT Scan Files and RPT Estimation Analysis Ms. A S Priyadarshini, Mr. Y.S.P Murthy, Mr. S. G. P. Raju, Mr. N.S.S Abhiram
Rapid Prototyping (RP) is an emerging technology, especially in a Three-Dimensional Printing (3DP) application. 3DP is used in many fields such as aeronautical, automotive, architecture, medical, and many others. 3DP can be effectively used in anatomical education for medical students who are pursuing their undergraduate degrees. It can also be used for pre-operative surgical planning by experts before surgery
Development and Reconstruction of Spinal Cord from CT Scan Files and RPT Estimation Analysis
Ms. A S Priyadarshini, Mr. Y.S.P Murthy, Mr. S. G. P. Raju, Mr. N.S.S AbhiramDevelopment and Reconstruction of Spinal
-
Experimental Analysis on Optimization of Process Parameters in Fused Deposition Modelling Mr. S. Hima Teja Reddy, Mr. CH. Veera Yaswanth Kumar, Mr. K. Manikya Chakradhar, Mr B. Teja Sai Trinadh
The 3D printing process is a kind of additive manufacturing, that the basic principle of this process is adding material layer by layer to form a product. The purpose of this research was to study the effect of orientation and internal over hangs on micro heat exchanger. In this we are optimizing the printing orientation to avoid the warpage of micro heat exchanger printing and decreasing the ovality of the circular tube by orienting
Experimental Analysis on Optimization of Process Parameters in Fused Deposition Modelling
Mr. S. Hima Teja Reddy, Mr. CH. Veera Yaswanth Kumar, Mr. K. Manikya Chakradhar, Mr B. Teja Sai TrinadhExperimental Analysis on Optimization
-
Experimental Investigation of Surface Finish Enhancement of Fused Deposition Modelled Parts Mr. A. Lokesh, Mr. M. Suresh, Mr. P. Guna Sagar, Mr. G. Satya Sai, Mr. S. Ananda Rayudu
3D printing is a promising digital manufacturing technique that produces parts with layer by layer. The influence of process parameters is investigated for PLA material in fused deposition modelling (FDM). This work aimed to determine what are the printing process parameters effect the surface roughness of printing parameters. Major influencing parameters are wall count, top and bottom closing layers effecting the surface roughness
Experimental Investigation of Surface Finish Enhancement of Fused Deposition Modelled Parts
Mr. A. Lokesh, Mr. M. Suresh, Mr. P. Guna Sagar, Mr. G. Satya Sai, Mr. S. Ananda RayuduExperimental Investigation of Surface
-
Reconstruction of Knee Joint by Using 3 Matics and Mimics and Design Mr.P. Jayakanth, Mr. P.S.S. Ganesh, Mr. P. Sandeep, Mr. V.Sandeep, Ms. P. Geetha Sri
The mechanical stress determination in human femur bone is of great importance in both research and clinical practice. One of the methods to estimate stress is through finite element modeling. In spite of that, the modeling technique has to be validated by an experimental approach as it is the best tool to access the accuracy of finite element model predictions. However, in the previous studies, this validation
Reconstruction of Knee Joint by Using 3 Matics and Mimics and Design
Mr.P. Jayakanth, Mr. P.S.S. Ganesh, Mr. P. Sandeep, Mr. V.Sandeep, Ms. P. Geetha SriReconstruction of Knee Joint
-
A Computational Fluid Dynamics Study and Heat Transfer in A Micro Channel Mr. M. Kiran Kumar, Mr. Hemanth Kumar, Mr. M.Sai Srinivas, Mr. I.Sanjay Abinav, Mr. S.Nookesh Kumar, Mr. M Sunil Raj, Dr BSV Ramarao
A theoretical study of single phase microchannel heat exchanger has been carriedout. The computational fluid dynamics (CFD) model equations are solved to predict the hydrodynamic and thermal behaviour of the exchanger. The geometry of the problem and meshing of it have been made in ANSYS Workbench. The models have been solved by ANSYS Fluent 12.0 solver. The utility of nonmaterial as a heat enhancer has been justified
A Computational Fluid Dynamics Study and Heat Transfer in A Micro Channel
Mr. M. Kiran Kumar, Mr. Hemanth Kumar, Mr. M.Sai Srinivas, Mr. I.Sanjay Abinav, Mr. S.Nookesh Kumar, Mr. M Sunil Raj, Dr BSV RamaraoA Computational Fluid Dynamics
-
Performance Improvement of an Organic Rankine Cycle with Low Grade Thermal Energy Mr. C. Chakravarthi, Mr. K Krishna Sai, Mr. K Mani Teja, Mr. M P Chowdary, Mr. S Manikanta, Ms. M Amrutha, Mr. GVN Santosh
Solar energy collectors have been the need of the hour for the past couple of decades as the world has been desperately trying to find new and innovative ways to shift the dependency on fossil fuel to clean and green energy sources for power generation. The aim of the present study is two folds modelling of “Compound Parabolic Collector” and studying its contribution in the performance improvement of “Organic Rankine Cycle”
Performance Improvement of an Organic Rankine Cycle with Low Grade Thermal Energy
Mr. C. Chakravarthi, Mr. K Krishna Sai, Mr. K Mani Teja, Mr. M P Chowdary, Mr. S Manikanta, Ms. M Amrutha, Mr. GVN SantoshPerformance Improvement of an Organic
-
Design and Analysis of Aircraft Telescopic Wing and Material Optimization Mr. D. Sandeep Datta, Mr.M.Mukesh Rama Krishna, Mr. Y.Lakshmi Narendra, Mr. G.Sudheer, Mr. B.Venkata Prasanna Krishna, Mr. A Yeswanth, Mrs. K Aravinda
The development of morphing wing technologies for flight regime adaptation has received great interest from Researchers and engineers in the past years. This paper is in one such research where we have designed a morphing wing structure to our aircraft to adaptive mechanisms and structures. Morphing can encompass many aspects of the aircraft design, including the location, shape, area and angle of the wings, tail or fuselage
Design and Analysis of Aircraft Telescopic Wing and Material Optimization
Mr. D. Sandeep Datta, Mr.M.Mukesh Rama Krishna, Mr. Y.Lakshmi Narendra, Mr. G.Sudheer, Mr. B.Venkata Prasanna Krishna, Mr. A Yeswanth, Mrs. K AravindaDesign and Analysis of Aircraft Telescopic
-
Reconstruction, Segmentation and Smoothing of Tibia and Fibula Mr. K. Vishnu Kalyan, Mr. N. Manikanta, Mr. V. Lakshmi Kumar, Mr. Md. Nawaz Shariff, Mr. K. Yogesh, Mr. DJ Johnson, Mrs. K Aravinda
Medical images are essential tools for medical practitioner and specialists to use when diagnosing problems and diseases in the body. These images from CT and MRI scans are converted into 3D CAD model and based on 3D model, reconstruction of knee joint is being made for medical applications. Hence, in this paper an attempt is made to create a 3D reconstructed anatomy structure based on real medical images of a patient
Reconstruction, Segmentation and Smoothing of Tibia and Fibula
Mr. K. Vishnu Kalyan, Mr. N. Manikanta, Mr. V. Lakshmi Kumar, Mr. Md. Nawaz Shariff, Mr. K. Yogesh, Mr. DJ Johnson, Mrs. K AravindaReconstruction, Segmentation and Smoothing
-
Product Design and Development Using 3D Technology By Fused Deposition Modelling Mr. V.V.D. Abhishek, Mr. P. Sai Krishna, Mr. A. Niranjan, Mr. S. Kowshik Durga Sai, Mr.P.Ramu, Ms. K Tulasi, Mr. S Srikanth
3D printing is a form of additive manufacturing technology where a three-dimensional object is created by laying down successive layers of material. It is also known as rapid prototyping, is a mechanized method whereby 3D objects are quickly made on a reasonably sized machine connected to a computer containing blueprints for the object. The 3D printing concept of custom manufacturing is exciting to nearly everyone
Product Design and Development Using 3D Technology By Fused Deposition Modelling
Mr. V.V.D. Abhishek, Mr. P. Sai Krishna, Mr. A. Niranjan, Mr. S. Kowshik Durga Sai, Mr.P.Ramu, Ms. K Tulasi, Mr. S SrikanthProduct Design and Development
-
CFD Analysis of Heat Transfer in A Double Pipe Heat Exchanger Using Fluent Mr. Allam Bhima Dhanaraju, Mr. Yandra Bharath Kalyan, Mr. Naidu Satish, Mr. Pemmadi Prabhuraju, Mr. Medaballi Ramkarthik, Mr. B Hari Krishna, Mr DJ Johnson
Numerical analysis of 3-d incompressible flow is done for concentric tubular heat exchanger type of domain; this is basically water to water heat exchanger. Analysis is done for both parallel flow and counter flow with different mass flow rate and when we compare the efficiency, efficiency is higher for counter flow and less for the parallel flow because in counter flow we have highest heat transfer area than in parallel flow
CFD Analysis of Heat Transfer in A Double Pipe Heat Exchanger Using Fluent
Mr. Allam Bhima Dhanaraju, Mr. Yandra Bharath Kalyan, Mr. Naidu Satish, Mr. Pemmadi Prabhuraju, Mr. Medaballi Ramkarthik, Mr. B Hari Krishna, Mr DJ JohnsonCFD Analysis of Heat Transfer
-
Design and Topology Optimisation of Truck Chasis for Maximum Stiffness Mr. G. Williams Babu, Mr. P. Sathish, Mr. P. D M Satya Sai Vara Prasad, Mr. S. Mani Kiran, Mr. G. Sri Satya Sai Narasimha Raju, Mr. S Srikanth, Dr G Avinash
Automotive chassis is an important part of an automobile. The chassis serves as a frame work for supporting the body and different parts of the automobile. Also, it should be rigid enough to withstand the shock, twist, vibration and other stresses. Along with strength, an important consideration in chassis design is to have adequate bending stiffness for better handling characteristics. So, maximum stress, maximum equilateral stress
Design and Topology Optimisation of Truck Chasis for Maximum Stiffness
Mr. G. Williams Babu, Mr. P. Sathish, Mr. P. D M Satya Sai Vara Prasad, Mr. S. Mani Kiran, Mr. G. Sri Satya Sai Narasimha Raju, Mr. S Srikanth, Dr G AvinashDesign and Topology Optimisation
-
CFD Analysis of a Finned Vertical Tube with Different Cross Sections Mr. Allu Subramanyam, Mr. Manga Veera Chandra Sekhar, Mr. Chikkala Vinayak, Mr. Seeli Praveen Kumar, Mr. Pitta Daante, Mr. B Bharath Kumar, Mr. N Raghuveer
The heat transfer rate to a fluid flowing in pipe can be enhanced by the use of internal fins. This work concerned with simulation analysis of vertical tube with helical fins used to enhance their heat transfer performance subjected to natural convection heat transfer. All the main parameters which can significantly influence the heat transfer performance of finned tube has been analyzed. Natural convection in a vertical tube
CFD Analysis of a Finned Vertical Tube with Different Cross Sections
Mr. Allu Subramanyam, Mr. Manga Veera Chandra Sekhar, Mr. Chikkala Vinayak, Mr. Seeli Praveen Kumar, Mr. Pitta Daante, Mr. B Bharath Kumar, Mr. N RaghuveerCFD Analysis of a Finned Vertical Tube
-
Thermal Analysis of Solar Air Heater Using CFD as A Tool Mr. P. Rakesh, Mr. N. Satish kumar, Mr. S. Surya Dileep, Mr.V. Sandeep Kumar, Mr. R. Siva Narendra, Mr. VVN Sarath, Mr. GVN Santosh
Solar air heating is a solar thermal technology in which the energy from the sun is captured by an absorbing medium and used to heat air. Solar air heater including a housing having a transparent front wall and an inlet and outlet for establishing a flow path for a gas such as air to be heated. An attempt has been made to carry out CFD based analysis using FLUENT to fluid flow and heat transfer characteristics of solar air heater
Thermal Analysis of Solar Air Heater Using CFD as A Tool
Mr. P. Rakesh, Mr. N. Satish kumar, Mr. S. Surya Dileep, Mr.V. Sandeep Kumar, Mr. R. Siva Narendra, Mr. VVN Sarath, Mr. GVN SantoshThermal Analysis of Solar Air Heater
-
Design and Analysis of Three Plate Injection Mould Mr. Nathipam Ganesh, Mr. Tirumalanaduni Sandeep, Mr. Mattaparthi Eswar Rao, Mr. Busi Veera Venkata Sai Ram, Mr. Vusa Mohana Surya Ganesh, Mr. P Ram Prasad, Mr. S Srikanth
The objective of this paper is to design a three-plate injection mould that used to produce thedifferentialcover components which are used in automobile. In the proposed workwe are trying to design injection mould that has the capacity to produce thin walled plastic components without warpage defect and also a mould which permits the part to be created in new plane away from gating system to allow sufficient cooling time
Design and Analysis of Three Plate Injection Mould
Mr. Nathipam Ganesh, Mr. Tirumalanaduni Sandeep, Mr. Mattaparthi Eswar Rao, Mr. Busi Veera Venkata Sai Ram, Mr. Vusa Mohana Surya Ganesh, Mr. P Ram Prasad, Mr. S SrikanthDesign and Analysis of Three Plate
-
Modelling and Mass Optimization of CNC Machine Arbor for Maximum Cutting Force Mr. D.Venkata Surya Sai, Mr S. Venkatesh, Mr G. Sri Ram Prasad, Mr R. Lalith Kishan, Mr. C. Yuvaraj Prasad, Mrs. P Gayatri, Mrs. K Aravinda
Traditionally, the design field has been identified with particular end products, e.g., mechanical design, electrical design, ship design. In these fields, design work is largely based on specific techniques to foster certain product characteristics and principles. The scope of this work includes, to design, model and simulate the CNC arbor, to optimize the cutting tool arbor for maximum stiffness condition and also to detailed factor safety in design
Modelling and Mass Optimization of CNC Machine Arbor for Maximum Cutting Force
Mr. D.Venkata Surya Sai, Mr S. Venkatesh, Mr G. Sri Ram Prasad, Mr R. Lalith Kishan, Mr. C. Yuvaraj Prasad, Mrs. P Gayatri, Mrs. K AravindaModelling and Mass Optimization of CNC
-
CFD Analysis of Whale Inspired Hydrofoil with Different Angles of Attack Mr. K.Joseph, Mr. V.Pradeep, Mr. K. Dileep kumar, Mr. B.Nikhil Varma, Mr. C.Naveen Sapthagiri, Ms. M Amrutha, Mr. DJ Johnson
Recent discoveries in the biomimicry field found that mimicking Humpback whale flippers can give us better Drag and Lift coefficients. CFD analysis is done on whale inspired modified NACA-0021 foil with sinusoidal leading edge. And Velocity and pressure contours are generated to see the results.It has found that with the change in the angle of attack of each foil the velocity contour changes
CFD Analysis of Whale Inspired Hydrofoil with Different Angles of Attack
Mr. K.Joseph, Mr. V.Pradeep, Mr. K. Dileep kumar, Mr. B.Nikhil Varma, Mr. C.Naveen Sapthagiri, Ms. M Amrutha, Mr. DJ JohnsonCFD Analysis of Whale Inspired Hydrofoil
-
Optimization of Support Structures to Avoid the Lift Off of Printing Component Mr. Dindi Naga Prashanth, Mr. Medisetti Sunil Kumar, Mr. Putta Surya Bhagavan, Mr. Thotakura Pavan, Mr. B Bharath Kumar, Mr. M Sunil Raj
Additive manufacturing is rapidly growing technology in the field of production and research. AM is perceived as an environmentally friendly and sustainable technology and has already gained a lot of attention globally. The potential freedom of design offered by AM is, however, often limited when printing complex geometries due to an inability to support the stresses inherent within the manufacturing process
Optimization of Support Structures to Avoid the Lift Off of Printing Component
Mr. Dindi Naga Prashanth, Mr. Medisetti Sunil Kumar, Mr. Putta Surya Bhagavan, Mr. Thotakura Pavan, Mr. B Bharath Kumar, Mr. M Sunil RajOptimization of Support Structures to Avoid
-
Design and Analysis of Screw Operated Gripper and RPT Estimation Mr. G.Vishnu Vardhan Sri Raj, Mr. P.Arun Kumar, Mr. P Jagadeesh Varma, Mr. G.Rajkumar, Mr. G.Akhil
The objective of the paper is to build a three fingered gripper for a flexible robotic arm to have the capability of mimic the motion of a snake such that work space of the robotic arm is maximized. In this paper a three fingered gripper is designed with payload capacity of 2kg by considering flexible design, ease of manufacture, low cost and recyclable material as the constraints. The designing of three fingered gripper is done in AUTODESK FUSION360
Design and Analysis of Screw Operated Gripper and RPT Estimation
Mr. G.Vishnu Vardhan Sri Raj, Mr. P.Arun Kumar, Mr. P Jagadeesh Varma, Mr. G.Rajkumar, Mr. G.AkhilDesign and Analysis of Screw Operated
-
Design, Modelling and Analysis of Front Wheel Assembly of Baja SAE Vehicle Mr. M. Venkata Swaroop, Mr. P. Veerendra, Mr. Y. Sai Charan, Mr. G. Sai Teja, Mr. S. Siva Sai Ram
The purpose of the Society of Automotive Engineers (SAE) Baja Major Qualifying Project (MQP) was to analyze the pre-existing Baja SAE (BSAE) vehicles to determine flaws and design a new chassis that improved upon the previous designs. This MQP identified particular problems with the size of the engine compartment, the overall suspension alignment and attachment points, as well as the visibly crooked nature of the vehicle.
Design, Modelling and Analysis of Front Wheel Assembly of Baja SAE Vehicle
Mr. M. Venkata Swaroop, Mr. P. Veerendra, Mr. Y. Sai Charan, Mr. G. Sai Teja, Mr. S. Siva Sai RamDesign, Modelling and Analysis of Front
-
Design and Analysis of Aircraft Engine Cooling Fan Mr. R. Vinay, Mr. R. Leela Satish Kumar, Mr. J. Durga Vara Prasad, Mr. T. Anish, Mr. K. Gowri Shankar
The current work is aimed to design an aircraft engine cooling fan. the family of turbo machines and they move air or gas conns belong continuously at desired velocity by action of a rotor. Flow investigation of the fan is planned to be carried out by using ANSYS-FLUENT software for different designed off design points of operation. The performance of the fan generated from the CFD analysis at the design point will be compared
Design and Analysis of Aircraft Engine Cooling Fan
Mr. R. Vinay, Mr. R. Leela Satish Kumar, Mr. J. Durga Vara Prasad, Mr. T. Anish, Mr. K. Gowri ShankarDesign and Analysis of Aircraft Engine Cooling Fan
-
Thermal Analysis of Engine Cylinder Fins to Optimize the Shape to Improve the Heat Transfer Rate Mr. N. Raghuram, Mr. K. Sandeep Kumar, Mr. V.S.S.S. Sumanth, Mr. M. Avinash, Mr. A.Sumanth
The Engine cylinder is one of the major automobile components, which is subjected to high temperature variations and thermal stresses. In order to cool the cylinder, fins are provided on the surface of the cylinder to increase the rate of heat transfer. By doing thermal analysis on the engine cylinder fins, it is helpful to know the heat dissipation inside the cylinder. We know that, by increasing the surface area
Thermal Analysis of Engine Cylinder Fins to Optimize the Shape to Improve the Heat Transfer Rate
Mr. N. Raghuram, Mr. K. Sandeep Kumar, Mr. V.S.S.S. Sumanth, Mr. M. Avinash, Mr. A.SumanthThermal Analysis of Engine Cylinder Fins
-
Geometry and Location Optimization of Wavy Flag to Improve the Heat Transfer Rate Vortex Generator Mr G.D.N.Manikanta, Mr. D.B.M.Umasurya, Mr V.Suneel, Mr. C.Murali Krishna, Mr. P.Arun Kumar
This work demonstrates the effect of different shapes and positions of a wavy flag vortex generator on the heat transfer in a rectangular channel using Computational Fluid Dynamics (CFD) analysis. It covers the shape optimization as well as the position optimization of the shape optimized flag to achieve the best heat transfer enhancement. The result of post analysis shows that the shape optimized flag is the combination
Geometry and Location Optimization of Wavy Flag to Improve the Heat Transfer Rate Vortex Generator
Mr G.D.N.Manikanta, Mr. D.B.M.Umasurya, Mr V.Suneel, Mr. C.Murali Krishna, Mr. P.Arun KumarGeometry and Location Optimization
-
Forced Convection Studies with Different Geometries in Tube Bank Arrangement Using CFD Mr. M. Naga Krishna, Mr. P. Karthik, Mr B. Ajay Kumar, Mr G.D.V. Manoj, Mr N. Chaitanya Teja
Heat transfer to or from a bank (or bundles) of tubes in cross flow heat exchanger is relevant to numerous industrial applications; such as, steam generation in a boiler or air cooling in the coil of an air conditioner. The purpose of this research work is to find out the effect of horizontal pitch on the Nusselt number and friction factor of tube. The compact tube bank arrangement experiences high convective resistance on air side.
Forced Convection Studies with Different Geometries in Tube Bank Arrangement Using CFD
Mr. M. Naga Krishna, Mr. P. Karthik, Mr B. Ajay Kumar, Mr G.D.V. Manoj, Mr N. Chaitanya TejaForced Convection Studies with Different
-
Effect of layer height on final dimensional accuracy of SLM printing machine Mr. P.Shalem Kumar, Mr. D.Padmadora, Mr. M.Satish, Mr. Sk.Imran, Mr. S.Champak Sai Sri
Selective laser melting technology which rapidly growing technology in the additive manufacturing process. Additive manufacturing is influenced by so many parameters majorly laser power, scan speed, scanning strategy, layer height, support structure, laser diameter, hatch space etc. These are the various parameters which may influence properties of the resulting part. To study the influence of layer height on the final part
Effect of layer height on final dimensional accuracy of SLM printing machine
Mr. P.Shalem Kumar, Mr. D.Padmadora, Mr. M.Satish, Mr. Sk.Imran, Mr. S.Champak Sai SriEffect of layer height on final
-
3D Printing Thermo-Mechanical Analysis of Carburettor for Optimized Support Structure Mr. R. Vinay Kumar, Mr E. Sandeep, Mr U. Manikanta Swamy, Mr N. Sai Nilekh, Mr P. Veera Venkata Kojushik
Carburettor manufacturing is one of the challenging manufacturing process which takes high production time. This can be reduced with great interest if we take manufacturing in to account. Here we would like to manufacture the carburettor by using metal LPBF process. Metal AM process is rapidly growing technology. In metal AM process the complexity of the object is not considered. The quality of the final printed parts
3D Printing Thermo-Mechanical Analysis of Carburettor for Optimized Support Structure
Mr. R. Vinay Kumar, Mr E. Sandeep, Mr U. Manikanta Swamy, Mr N. Sai Nilekh, Mr P. Veera Venkata Kojushik3D Printing Thermo-Mechanical Analysis
-
Optimization of Laser Power to Avoid the Thermal Stress in The Metal Am Process Mr. K. Sai Vinay, Mr. D R K Subrahmanyam, Mr. V Tarun Kumar, Mr. K Meher Venkat
This investigation uses a complex geometry which combines both straight edges and a rounded feature, allowing for the in-depth analysis of the effects of laser power on Ti-6Al-4V alloy parts produced by additive manufacturing. The printing study was carried out using the laser beam powder bed fusion technique (SLM 280 HL). The laser power was altered in the range of 500 to 600 W, in order to evaluate the effects
Optimization of Laser Power to Avoid the Thermal Stress in The Metal Am Process
Mr. K. Sai Vinay, Mr. D R K Subrahmanyam, Mr. V Tarun Kumar, Mr. K Meher VenkatOptimization of Laser Power
-
Effect of Layer Height and Printing Speed on Print Time Estimation and Cost Analysis Mr. N. Venkat, Mr.N. Durga Prasad, Mr. P. Sai Manoj, Mr. Y. Satish, Mr. T. Raj Kumar
The 3D printing process is a kind of additive manufacturing, that the basic principle of this process is adding material layer by layer to form a product. The purpose of this research was to study the effect of layer thickness and printed speed on CNC cutting tool for making casting replica. In this we are varying the layer thickness and printing speed on material consumption and printing speed. In this study by varying
Effect of Layer Height and Printing Speed on Print Time Estimation and Cost Analysis
Mr. N. Venkat, Mr.N. Durga Prasad, Mr. P. Sai Manoj, Mr. Y. Satish, Mr. T. Raj KumarEffect of Layer Height and Printing
-
Design and Analysis of an Uneven Terrain Freight Transportation Mechanism Mr. T. Tilak Sai, Mr. M. S. S. Markandeya Swamy, Mr. K. Praveen Srinivas, Mr. Y. V. S. Harsha
Wheels are optimal only in highly selective sites or limited artificial environment that we purposefully design to allow wheeled locomotion. They exhibit poor performance in variable terrain and is subjected to large scale wear and tear. Using idea of Theo Jansen’s kinetic sculptor this paper aims to create a legged mechanism which can be used as an alternate for tyres over rough terrains. It is an 8-bar mechanism
Design and Analysis of an Uneven Terrain Freight Transportation Mechanism
Mr. T. Tilak Sai, Mr. M. S. S. Markandeya Swamy, Mr. K. Praveen Srinivas, Mr. Y. V. S. HarshaDesign and Analysis of an Uneven Terrain
-
Design and Rigid Dynamic Analysis of Engine Cylinder with Integrated Mass Optimization Mr. S. Satish Kumar, Mr. K. Varun Kumar, Mr.I. Ravindra, Mr. S.S.V. Varun Kumar
The connecting rod is the intermediate member between the piston and the Crankshaft. Its primary function is to transmit the push and pull from the piston pin to the crank pin, thus converting the reciprocating motion of the piston into rotary motion of the crank. This paper describes designing and Analysis of connecting rod. Currently, existing connecting rod is manufactured by using Forged steel
Design and Rigid Dynamic Analysis of Engine Cylinder with Integrated Mass Optimization
Mr. S. Satish Kumar, Mr. K. Varun Kumar, Mr.I. Ravindra, Mr. S.S.V. Varun KumarDesign and Rigid Dynamic
-
Design and Simulation of Disc Brake Rotor by Using Taguchi Analysis to Study Mr. A. V. Ravi Kiran, Mr. K. Srinivas Trigun, Mr. K. Shekhar, Mr. S. Bharath Kumar
Braking system is the major part of the vehicle in order to slow down and stop the vehicle. Disc brakes were most popular on sports cars when Disc brakes were first introduced, since these vehicles are more demanding about brake performance. Disc brakes are more common form in most passenger vehicles, although many (particularly light weight vehicles) use drum brakes on the rear wheels to keep costs and weight down as well as to simplify.
Design and Simulation of Disc Brake Rotor by Using Taguchi Analysis to Study
Mr. A. V. Ravi Kiran, Mr. K. Srinivas Trigun, Mr. K. Shekhar, Mr. S. Bharath KumarDesign and Simulation of Disc
-
Determination of Optimum Scanning Speed to Regulate Performance Characteristics of Spur Mr Nakka Chakravarthi, Mr Dusarlapudi Venkata Manohar, Mr Vullamparthy Marcus Paul
Gears are commonly used for transmitting power. They develop high stress concentration at the root and the point of contact. We have performed the 3D printing simulation to spur gears to study the effect of laser scanning speed on capturing the geometry and minimum stresses and displacements. The laser transferred energy decreased with the increase of scan speed, which cause more holes and cracks in the alloy
Determination of Optimum Scanning Speed to Regulate Performance Characteristics of Spur
Mr Nakka Chakravarthi, Mr Dusarlapudi Venkata Manohar, Mr Vullamparthy Marcus PaulDetermination of Optimum Scanning Speed
-
Structural Analysis of Earth Auger Bit Mr. B.Sri Harsha, Mr K.Gowtham, Mr V.H.V.S. Vinay, Mr. P.Dhanush, Mr R.Ramakrishna, Ms. M Amrutha, Mr M Sunil Raj
Earth Auger as we all know is a vital part in Drilling all Holes in the ground be that a simple hanging bar to one of the most complex rockets. Quite possibly the most important parts of Earth Auger are a Auger bit. So, it is vital to strengthen this important aspect to ready it for any use. Our fundamental objective behind this paper is to study the Earth Auger bit in detail while doing analysis using ANSYS
Structural Analysis of Earth Auger Bit
Mr. B.Sri Harsha, Mr K.Gowtham, Mr V.H.V.S. Vinay, Mr. P.Dhanush, Mr R.Ramakrishna, Ms. M Amrutha, Mr M Sunil RajStructural Analysis of Earth Auger Bit
-
Modeling and 3D Printing Simulation of Jet Engine Propeller with Minimum Printing Time Mr. P. Varaprasad, Mr. B. Venkata Abhinav, Mr. M.Sanjay kumar, Mr. S. Vamsi, Mr. U.Tarun
Turboprop motors are the class of motors that drives the air ship propeller. Turboprop comprises of propeller, blower, burning chambers, turbine, and a spout. It works with less speed, less cost, better eco-friendliness, low climbing pace, less ozone depleting substance discharge and less vibration. The propeller cutting edge and shaft are viewed as the basic pieces of a turboprop motor as they turn at high speeds
Modeling and 3D Printing Simulation of Jet Engine Propeller with Minimum Printing Time
Mr. P. Varaprasad, Mr. B. Venkata Abhinav, Mr. M.Sanjay kumar, Mr. S. Vamsi, Mr. U.TarunModeling and 3D Printing
-
Modelling and Structural Analysis of Pelton Wheel Turbine at Maximum Load Condition Mr. S. Chandra Kiran, Mr. T.D. Satyanarayana, Mr. K. Mani Sridhar, Mr. N. Naga Sai
A Pelton turbine bucket is the individual component which makes up the turbine section of a pelton turbine. The blades are responsible for extracting energy from the high pressure water produced by the nozzle jet. The pelton buckets are very often the limiting component of pelton turbines. To survive in this difficult environment, blades often use exotic materials. In this paper a pelton turbine bucket is designed and Modeled in 3D modeling
Modelling and Structural Analysis of Pelton Wheel Turbine at Maximum Load Condition
Mr. S. Chandra Kiran, Mr. T.D. Satyanarayana, Mr. K. Mani Sridhar, Mr. N. Naga SaiModelling and Structural Analysis
-
Design and Modelling of Francis Turbine by Using Generative Shape Design Mr. M. Sai Praneeth, Mr. D. Ravi Varma, Mr. A. Madhu, Mr. P. Noel Ratnakar, Mr. G. Phanindra
The Francis turbine is a type of water turbine. It is an inward-flow reaction turbine that combines radial and axial flow concepts. Francis turbines are the most common water turbine in use today and can achieve over 95% efficiency. Francis turbines are primarily used for electrical power production. The power output of the electric generators generally ranges from just a few kilowatts up to 1000 MW, though mini-hydro
Design and Modelling of Francis Turbine by Using Generative Shape Design
Mr. M. Sai Praneeth, Mr. D. Ravi Varma, Mr. A. Madhu, Mr. P. Noel Ratnakar, Mr. G. PhanindraDesign and Modelling of Francis Turbine
-
Optimization of printing process parameters to avoid the plastic strain during the printing Mr. PVVG Pavan Kumar, Mr. Ch Srikar, Mr. I Teja srinivas, Mr. G Pavan satya kumar
The problem of designing a compact high-performance evaporator for miniature refrigeration system has been investigated. Micro cooling channel has multiple applications to transfer the heat and cool the system. To manufacture these micro channels through conventional machining is very difficult to overcome these problems we choose Additive manufacturing to manufacture the model. We choose SLM 280HL printer to simulate the model
Optimization of printing process parameters to avoid the plastic strain during the printing
Mr. PVVG Pavan Kumar, Mr. Ch Srikar, Mr. I Teja srinivas, Mr. G Pavan satya kumarOptimization of printing process
-
Modelling and Material Optimization of Piston Head to Sustain the Higher Load Mr. M Devi vara Prasad, Mr. M Divakar, Mr. K Ajay Kumar, Mr. T Surya Kumar, Mr. M Arbaaz
Engine pistons are one of the most complex components among all automotive and other industry field components. The engine can be called the heart of a vehicle and the piston may be considered the most important part of an engine. There are lots of research works proposing, for engine pistons, new geometries, materials and manufacturing techniques, and this evolution has undergone with a continuous improvement.
Modelling and Material Optimization of Piston Head to Sustain the Higher Load
Mr. M Devi vara Prasad, Mr. M Divakar, Mr. K Ajay Kumar, Mr. T Surya Kumar, Mr. M ArbaazModelling and Material Optimization
-
Reconstruction and Modelling of Hip Joint by Using 3D Slicer and Rapid Prototyping Mr. Ch. Ramesh, Mr. K. Prudhvi Sai, Mr. M.Veera Pradeep, Mr. T. Krishna Mohan
The use of three-dimensional (3D) printing is becoming more common, including in the field of orthopaedic surgery. There are currently four primary clinical applications for 3D-printing in hip and pelvic surgeries: (i) 3D-printed anatomical models for planning and surgery simulation, (ii) patient-specific instruments (PSI), (iii) generation of prostheses with 3D-additive manufacturing, and (iv) custom 3D-printed prostheses
Reconstruction and Modelling of Hip Joint by Using 3D Slicer and Rapid Prototyping
Mr. Ch. Ramesh, Mr. K. Prudhvi Sai, Mr. M.Veera Pradeep, Mr. T. Krishna MohanReconstruction and Modelling of Hip
-
Mass Optimization of Braking Pedal and Simulating 3D Metal Printing Process to Study Mr. K. Mani Suresh, Mr. M. Bhanu Prakash, Mr.B. Nirosh, Mr. K. Sasindra Manikanta
Safety aspect in automotive engineering has been considered as a number one priority in development of new vehicle. Each single system has been studied and developed in order to meet safety requirement. Instead of having air bag, good suspension systems, good handling and safe cornering, there is one most critical system in the vehicle which is brake systems The main objective of the paper is to design of brake pedal and optimizing
Mass Optimization of Braking Pedal and Simulating 3D Metal Printing Process to Study
Mr. K. Mani Suresh, Mr. M. Bhanu Prakash, Mr.B. Nirosh, Mr. K. Sasindra ManikantaMass Optimization of Braking Pedal
-
A Pure Thermal Analysis of 3D Printing for Different Laser Powers for Optimization Thermal Distribution Mr. N. Hema Sundar Bulliyya, Mr P. S V B Datta Varun, Mr G. V V S Narasimha, Mr K. Tarun
Engine pistons arrangement are one of the most complex components among all automotive and other industry field components. The engine can be called the heart of a vehicle and the engine head may be considered the most important part of an engine. There are lots of research works proposing, for engine pistons, new geometries, materials and manufacturing techniques, and this evolution has undergone
A Pure Thermal Analysis of 3D Printing for Different Laser Powers for Optimization Thermal Distribution
Mr. N. Hema Sundar Bulliyya, Mr P. S V B Datta Varun, Mr G. V V S Narasimha, Mr K. TarunA Pure Thermal Analysis of 3D Printing
-
Modelling and Topology Optimization of Car Rim to Reduce the Weight of the Wheel Mr. T. Dharmendra, Mr. S. Nazeem, Mr. K. Naveen Sai, Mr. J. Sudheer, Mr N. Siva Shankar
The wheel is a main mechanical term of the vehicular suspension system that supports the static and dynamic loads encountered during vehicle action. Since cars carry heavy loads of occupants as well as self-weight, the alloy wheel rim should be strong enough to withstand this load. Thus, their design should be done very cautiously. While designing such a main kind of automotive component taking care of protection.
Modelling and Topology Optimization of Car Rim to Reduce the Weight of the Wheel
Mr. T. Dharmendra, Mr. S. Nazeem, Mr. K. Naveen Sai, Mr. J. Sudheer, Mr N. Siva ShankarModelling and Topology Optimization
-
Design of Precision Steering Mechanism and Motion Study of Ackermann Steering Mechanism Mr. K. Sri Satya Sandeep, Mr. K. Praveen, Mr. K. Phani Kumar, Mr. N. Ram Pavan Kumar
Steering systems are used to change the direction of the vehicle. These are essential to provide vehicle safety, steering quality and steering control and used to turn the vehicle without loss of traction and also used to maintain the directional stability of the vehicle. The most commonly used steering geometries are Davis and Ackermann. The types of steering systems are trapezoidal; double trapezoidal and Rack & pinion etc
Design of Precision Steering Mechanism and Motion Study of Ackermann Steering Mechanism
Mr. K. Sri Satya Sandeep, Mr. K. Praveen, Mr. K. Phani Kumar, Mr. N. Ram Pavan KumarDesign of Precision Steering Mechanism
-
Design and Mass Optimization of Steering Arm for Metal Additive Manufacturing Mr. Ainapurapu M V Satya Sai Raghava Raja, Mr. Yadagani Bala Venkata Krishna, Mr Vasa Mohan Kumar
Steering systems are used to change the direction of the vehicle. These are essential to provide vehicle safety, steering quality and steering control and used to turn the vehicle without loss of traction and also used to maintain the directional stability of the vehicle. The most commonly used steering geometries are Davis and Ackermann. Steering arm is used for transmitting the turning force from the steering gear to the drag
Design and Mass Optimization of Steering Arm for Metal Additive Manufacturing
Mr. Ainapurapu M V Satya Sai Raghava Raja, Mr. Yadagani Bala Venkata Krishna, Mr Vasa Mohan KumarDesign and Mass Optimization
-
Design, Modeling & Simulation of A Thermoelectric Cooling System (TEC) Mr. Ch.Thiru Venkatesh, B. Keshav, M.Mohan Satya Sai Venkat, E.Poorna Sai, G.Nanda Babu
Thermoelectric Devices are solid state devices which directly convert thermal energy to electrical energy and vice versa. In the recent past, a lot of effort has been made to improve the performance and also the power generated by a thermoelectric device. This is done by attaching heat sinks on either sides of the device. Optimizing heat sinks improves the overall efficiency of it but on the other hand the device.
Design, Modeling & Simulation of A Thermoelectric Cooling System (TEC)
Mr. Ch.Thiru Venkatesh, B. Keshav, M.Mohan Satya Sai Venkat, E.Poorna Sai, G.Nanda BabuDesign, Modeling & Simulation
-
Buckling Analysis of Cantilever Twisted FGM Plate for Buckling Load and Non-Buckling Mr. E. Kiran, Mr. N. Uma Srinivasu, Mr. K. Trinadh, Mr. SK. S. H. J. Kareemulla Sha Khadari
The demand and application of composites are increasing nowadays. Composite materials in the form of plate or plate-like structures are widely used in wind turbine blades and ship building due to its high specific strength and stiffness. For high thermal applications, Functionally Graded Materials (FGM) are used in preference to laminated composites because of its good performance in the thermal field.
Buckling Analysis of Cantilever Twisted FGM Plate for Buckling Load and Non-Buckling
Mr. E. Kiran, Mr. N. Uma Srinivasu, Mr. K. Trinadh, Mr. SK. S. H. J. Kareemulla Sha KhadariBuckling Analysis of Cantilever
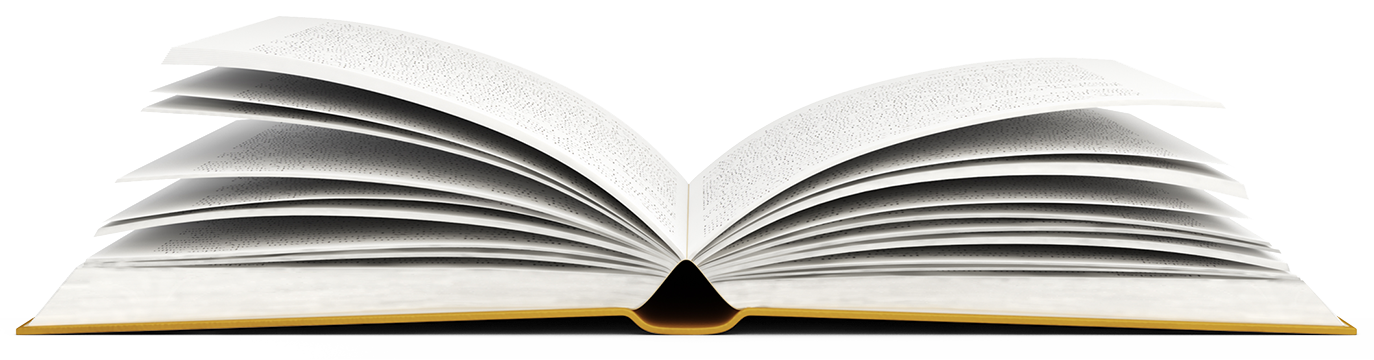